Counting stock by hand? That's getting really hard for businesses today. It doesn't matter if you have a warehouse, a retail shop, or sell online. How you handle your inventory can make a huge difference to your success. A smart move is switching to setting up a barcode inventory system, which helps keep stock accurate and lets your system grow as your business does.
Using an inventory list spreadsheet and following a few clear steps can make it easy to implement a barcode system for inventory. This guide shows you how and also shares tips to build a system that’s fast, reliable, and grows with you.
What Is a Barcode Inventory System?
An inventory barcode system uses barcode labels and scanners to track inventory movements. It integrates with software that logs product details, quantities, and locations in real-time.
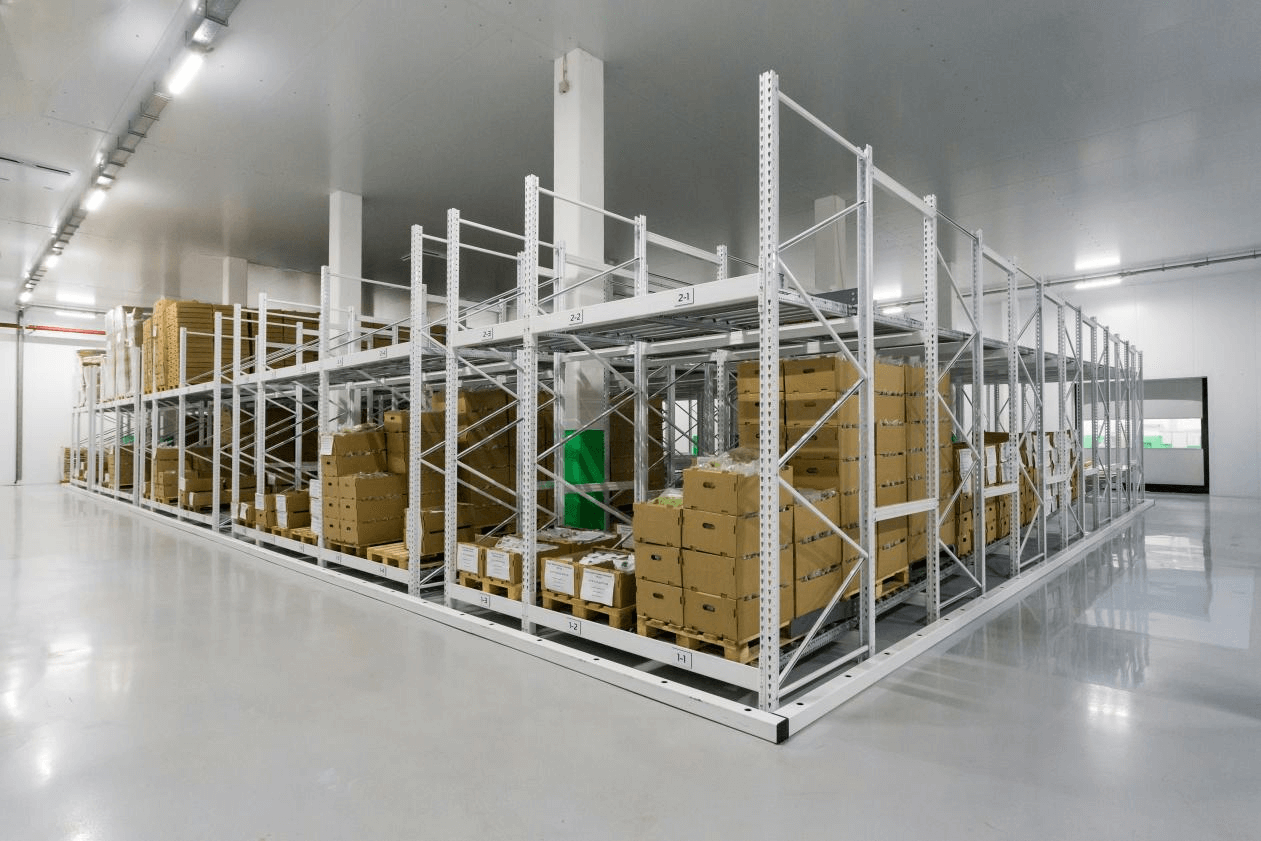
Essential Tools for a Barcode Inventory System Setup
Here’s what you’ll need to build a reliable barcode inventory tracking system:
Barcode Generator or Inventory Software
Tools to create unique barcodes for your products. Can range from online tools to integrated software features.
Barcode Labels
Physical labels to affix to products or shelves. Choose material based on environment (paper, synthetic, etc.).
Barcode Printers
Dedicated printers (thermal transfer or direct thermal) for creating clear, durable, and scannable labels.
Barcode Scanners or Mobile PDAs
Devices to read barcodes quickly and accurately. Options range from simple USB scanners to rugged mobile computers.
By digitizing your inventory tracking process, you’ll reduce manual errors, improve accuracy, and boost productivity.
Next, let's look at how to set up a barcoding inventory system step by step.
How to Set up a Barcode Inventory System
Prepare Your Inventory List Spreadsheet
The first step to building a barcode inventory system is to organize your product data in an inventory list spreadsheet, such as Excel, CSV files, or Google Sheets.
List each product with its name, SKU, variant (like size or color), categories, purchase cost, and quantity. This file will become the foundation for your barcode labels and inventory software integration.
Make sure your columns are clearly labeled and consistent—this will save you headaches later. You'll use this spreadsheet to generate and assign barcodes for every product variant you track.
Select the Right Barcode Format
Every item you stock needs a unique identifier. Usually, that's an SKU. Sometimes, it might be an SKU plus a batch number if you need more detail. This information can be encoded into a barcode.
Scan that barcode, and your system instantly knows what the item is. It keeps track of details, updates counts in real-time, and cuts down on mistakes when you sell, ship, or count inventory.
There are two main barcode formats: linear (1D) types like UPC, EAN, and Code 128, and 2D codes such as QR codes. So how do you choose the best one for inventory tracking?
For many businesses, especially small businesses and warehouses, Code 128 is a popular choice. It's free to use, widely supported by inventory systems, and offers high-density encoding—ideal for SKUs, batch numbers, or even bin locations in the inventory system.
Most standard scanners can read Code 128 easily, which helps keep your equipment costs lower. Plus, Code 128 codes don't have to be a specific length. You can make your item codes as long or short as you need.
However, keep this in mind: If you sell through big players like Amazon or Walmart, or if you might sell internationally later on, you should look into getting official GS1 barcodes (like GTINs or UPCs). You'll need to register for these. They are required to work smoothly with major retailers and across different supply chains.
Select Barcode Generation & Inventory Software
Once you've decided on the barcode type, you'll need software to generate and manage your inventory barcodes.
For businesses managing a limited number of SKUs, Excel combined with a free online barcode generator can be a practical solution for simple inventory tracking.
Of course, most businesses will still need to rely on dedicated inventory software. Some include built-in barcode creation tools, while others allow integration with third-party label design software like Bartender, and NiceLabel.
Look for features of inventory software like:
- Barcode Generation
- Customizable barcode templates
- Batch printing
- Database integration
- Mobile-friendly interfaces
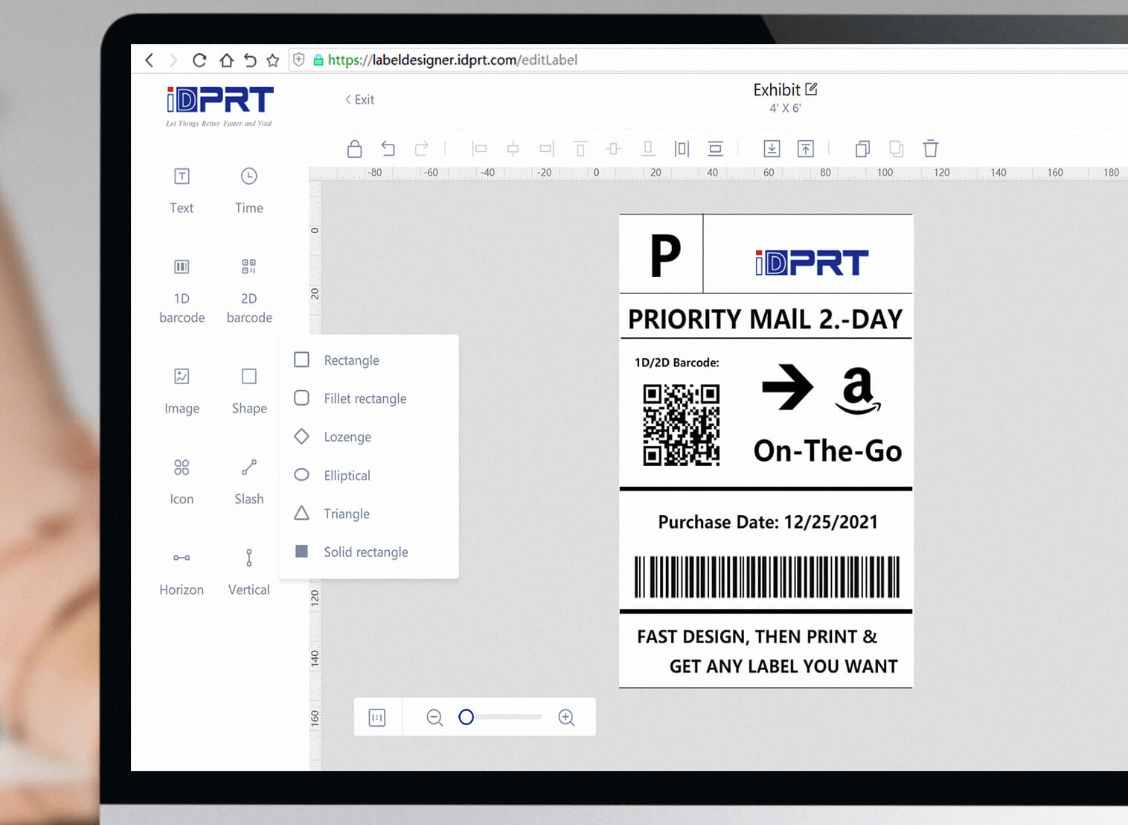
Generate and Print Inventory Barcode Labels
Alright, time to create your barcodes. You can use a free online barcode generator tool or specific barcode software for this. Then, print them out using a professional barcode printer.
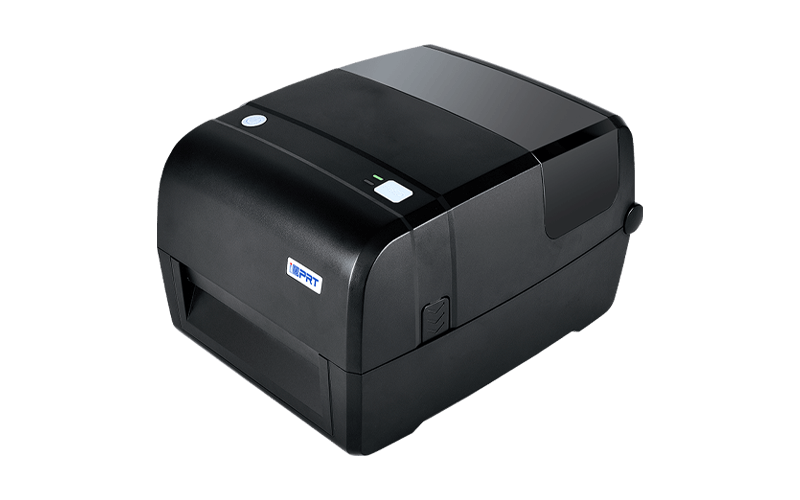
iT4X Thermal Transfer Barcode Printer
- Resolution: 203dpi, 300dpi
- Printing method: Direct Thermal and Transfer Thermal
- Max. print speed: 8ips @ 203dpi, 6ips @ 300dpi
- Max. print width: 4.25"(108mm) @ 203dpi and 4.17"(106mm) @ 300dpi
- Memory: 256 MB Flash / 128 MB RAM
Inventory software makes this step faster. You can upload your inventory list, weed out items you no longer sell (like discontinued or old products), and then print barcode labels for everything in batches.
Take the iDPRT iT4X, for instance. It's a high-performance 4-inch thermal transfer label printer. Perfect for making inventory tags, rack labels, and shelf labels. It handles continuous high-volume printing without overheating or slowing down, producing sharp, durable barcodes that scan perfectly.
The iT4X works with various thermal transfer label materials – paper, polyester, and synthetics. This thermal barcode printer connects via USB, Serial, Ethernet, and optional Wi-Fi and Bluetooth.
Plus, it comes with BarTender software. That means you're all set to design custom labels and automate your printing.
Small business or startup using Excel for inventory? No problem. Just import your inventory data into the barcode software. Batch printing your product barcodes becomes a breeze – super handy!
It's easy to integrate into any inventory system, from basic Excel setups to full WMS platforms. Ideal for businesses that demand speed, accuracy, and flexibility on the warehouse floor.
Pro tip:
- Pick the right labels: Use waterproof and abrasion-resistant labels for dusty, damp, or high-wear inventory environments to ensure durability and scannability.
- Test a few first: Print a small batch. Make sure the barcodes look good and scan perfectly before you print them all.
Label Your Inventory with Barcodes
Labels printed? Great. Next up: carefully put them on your products.
This might sound basic, but where you place the label is key. Make sure it's easy to see and reach for quick, accurate scans. This is especially true in busy spots like warehouses or retail stockrooms.
Try not to stick labels on curved bits, rough surfaces, or along seams. Scanners often have trouble reading them there.
You're almost done setting up your barcode system! Soon you'll be tracking, checking, and fine-tuning your inventory like a pro.
Important: Remember to do this for all new products that arrive.
Scan, Track, and Monitor Inventory
Barcodes are only useful if you have a scanner to read them—without it, they're just lines on a label. Barcode scanning equipment have various types, each suited for different operational needs:
- Smartphone + App: A smartphone with a barcode scanning app is ideal for small businesses or mobile inventory checks. It's cost-effective and easy to deploy, especially for low-frequency scanning tasks.
- Handheld Barcode Scanner: Faster, more accurate for routine warehouse tasks (receiving, shipping, restocking). Wireless ones connect to tablets or PCs, so no messy cables. You can move freely around workstations and shelves.
- PDA Scanner: A rugged, all-in-one handheld device that scans barcodes, processes data, and connects wirelessly. Really useful for big jobs like order picking, stock counts, and real-time inventory tasks on the warehouse floor.
Using these scanners for your inventory barcodes gives you real-time tracking. You'll see stock move from arrival to dispatch, making everything clearer across your operations.
Pro tip: If you’re using rugged PDAs or wireless scanners, just make sure they play nice with your inventory management system (IMS). Also, check they can read the types of barcodes you’re using.
Barcode Inventory System in Action
Once your barcode system for inventory management is in place, it becomes a powerful tool across inventory and supply chain operations. Here’s how to put it to work:
1. Inventory Tracking
Barcodes allow real-time tracking of item movement—whether it's transferring stock between warehouse zones or shipping products across the country. Every scan logs location changes, reducing the risk of misplaced items and speeding up retrieval when issues arise.
Pro tip: Scanning must be embedded in workflows. Train staff to scan on receipt, transfer, and dispatch to maintain traceability.
2. Inventory Optimization
Barcodes provide visibility into stock levels and item locations, which supports smarter warehouse layout decisions. Frequently picked items can be moved to accessible zones, reducing handling time and boosting efficiency.
Pro tip: Use inventory software and a barcode printer to batch print shelf labels and bin location barcodes. This simplifies storage zone identification, accelerates item scanning, and minimizes picking errors, especially in high-turnover or multi-zone warehouses.
3. Efficient Stock Audits
Barcode systems streamline inventory counts and cycle audits. Scanning is faster and significantly more accurate than manual entry, minimizing human error.
FAQs about Barcode Inventory System
1. Do I need special software to manage a barcode inventory system?
Yes, usually. You'll want inventory management software that can help you create barcodes, print out labels, and keep track of your stock in real time. Some systems even link up directly with barcode printers and mobile scanners to make things run very smoothly.
2. What’s the best barcode type for inventory management?
Code 128 is a very popular choice for inventory. It’s versatile – it can handle letters, numbers, and varying lengths. Plus, most standard barcode printers and scanners can read it without any trouble.
3. Can I use Excel with a barcode inventory system?
Absolutely. Many small businesses use Excel to organize inventory data and generate barcodes via online tools or integrated software. As your business scales, you may need to migrate to a full-featured IMS.
4. Do I need a special inventory barcode printer for inventory labels?
Yes, for the best results, a dedicated barcode label printer is the way to go. A printer like the iDPRT iT4X will give you crisp, clear labels that scan easily every time. This is especially important if you’re printing a lot of labels, say for a busy warehouse or a retail distribution hub.
5. What are the Common Mistakes of Inventory Barcode System to Avoid
- Using the wrong barcode type for your scanner
- Poor-quality printing or blurry labels
- Inconsistent label placement
- Not backing up inventory data
Avoid these pitfalls to ensure smooth implementation and long-term efficiency.
Implementing a barcode inventory system doesn’t have to be complex or expensive. With the right tools—especially a reliable barcode printer—you can achieve accurate tracking, faster workflows, and better control over your stock.
Ready to Upgrade Your Inventory System?
Choose the right barcode printer today. Start smart, print smart—upgrade your inventory system with iDPRT!